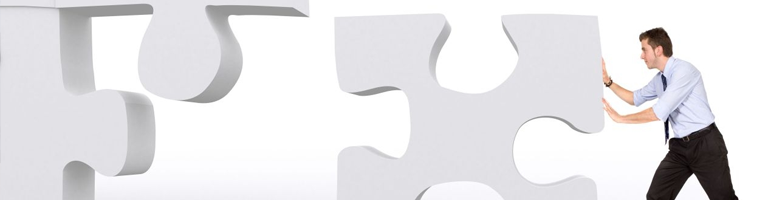
Advance PMS
APMS (Advanced Planned Maintenance System) is a software application that efficiently monitors, manages, and plans the maintenance of each vessel. Proper maintenance of onboard machinery ensures smoother operation, better logistic control, and reduced breakdown costs. APMS offers a cost-effective way to plan and schedule regular maintenance, outline correct work procedures, and maintain inventory for optimal store on board - which all helps maximize earnings for the ship owners. It also has provisions for budget allocation, full requisition to purchase process along with exhaustive graphical reporting and dashboard.
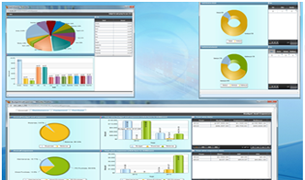
APMS Dashboard: Detail View
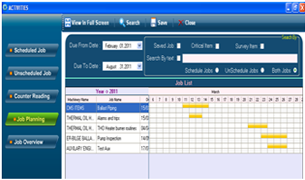
Vessel: Job Planning
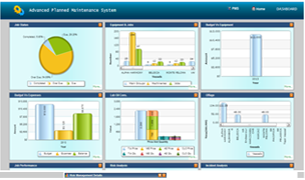
APMS Dashboard Home
How beneficial is it?
- Help in taking more factual and quicker decisions
- Create more space for maritime managers and leaders to assist in optimizing and utilizing resources for optimal maintenance of the vessels in time
- Increased productivity
- Value added quality information and business intelligence
- Direct impact on bottom line by optimizing costly maintenance
- Success with satisfaction
The Solution You Need
- Better allocation of resources: collecting data on spare parts and maintenance jobs has economic advantages in terms of inventory management and planning; allocate resource with greater efficiency when maintenance data is available for purchasing decisions and budget planning
- Save time: automatic migration of updated data from the vessel into the central database saves time and reduces communication costs as no human intervention is needed
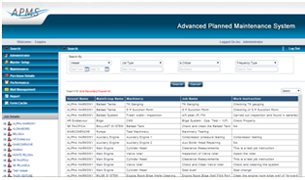
APMS Home
- Easier analysis: the system is risk and cost integrated: it checks equipment, activity, and personnel risks and quantifies the cost of these activities in financial calculations. This provides users with a powerful tool for analyzing and comparing operations
- Ensures quality: having the APMS on board is an essential part of the Quality Management System (QMS) as the whole process of maintaining a vessel is handled on a single, integrated platform. The application is also in compliance with the Interna¬tional Safety Management (ISM) Code
- Better evaluations and estimation: all work histories are stored and easily retrieved. This data can be used for risk and performance evaluations, and will offer ship owners an increasingly accurate description of ship cost/maintenance structures
Advance PMS
- Risk-based and cost based job evaluation
- Obtain various data: man-hours spent, riding team, shore support team, and man-hours used
- International Marine Purchasing Association (IMPA) and non-IMPA list integrated in the application
- Real-time tracking of stores and inventory
- Requisition raising processes and purchase
- MIS reports with business intelligence and graphical dashboard